Overview
This unit aims to develop extensive skills and knowledge in mechanical engineering design. You will learn mechanical design principles in a professional context, including requirements analysis, concept development, detailed design, fabrication, testing, evaluation, and reporting. You will develop skills in 2D drafting, 3D solid modelling, rendering, and producing detailed assembly drawings of mechanical components. Additionally, you will be introduced to machine elements such as gears, bearings, cams, couplings, flywheels, mechanical seals, and their applications in various engineering contexts. You will undertake a team-based design and build project, applying sustainable mechanical design principles learned in this unit using advanced manufacturing methods such as 3D printing. Lectures and workshop sessions will provide the necessary material and support for the successful completion of the project.
Details
Pre-requisites or Co-requisites
Prerequisites: ENEG11005: Fundamentals of Professional Engineering, ENEG11008: Materials for Engineers, and ENEM12009: Structural Mechanics.
Important note: Students enrolled in a subsequent unit who failed their pre-requisite unit, should drop the subsequent unit before the census date or within 10 working days of Fail grade notification. Students who do not drop the unit in this timeframe cannot later drop the unit without academic and financial liability. See details in the Assessment Policy and Procedure (Higher Education Coursework).
Offerings For Term 2 - 2025
Attendance Requirements
All on-campus students are expected to attend scheduled classes - in some units, these classes are identified as a mandatory (pass/fail) component and attendance is compulsory. International students, on a student visa, must maintain a full time study load and meet both attendance and academic progress requirements in each study period (satisfactory attendance for International students is defined as maintaining at least an 80% attendance record).
Recommended Student Time Commitment
Each 6-credit Undergraduate unit at CQUniversity requires an overall time commitment of an average of 12.5 hours of study per week, making a total of 150 hours for the unit.
Class Timetable
Assessment Overview
Assessment Grading
This is a graded unit: your overall grade will be calculated from the marks or grades for each assessment task, based on the relative weightings shown in the table above. You must obtain an overall mark for the unit of at least 50%, or an overall grade of 'pass' in order to pass the unit. If any 'pass/fail' tasks are shown in the table above they must also be completed successfully ('pass' grade). You must also meet any minimum mark requirements specified for a particular assessment task, as detailed in the 'assessment task' section (note that in some instances, the minimum mark for a task may be greater than 50%). Consult the University's Grades and Results Policy for more details of interim results and final grades.
All University policies are available on the CQUniversity Policy site.
You may wish to view these policies:
- Grades and Results Policy
- Assessment Policy and Procedure (Higher Education Coursework)
- Review of Grade Procedure
- Student Academic Integrity Policy and Procedure
- Monitoring Academic Progress (MAP) Policy and Procedure - Domestic Students
- Monitoring Academic Progress (MAP) Policy and Procedure - International Students
- Student Refund and Credit Balance Policy and Procedure
- Student Feedback - Compliments and Complaints Policy and Procedure
- Information and Communications Technology Acceptable Use Policy and Procedure
This list is not an exhaustive list of all University policies. The full list of University policies are available on the CQUniversity Policy site.
Feedback, Recommendations and Responses
Every unit is reviewed for enhancement each year. At the most recent review, the following staff and student feedback items were identified and recommendations were made.
Feedback from Unit evaluation
Students praised the unit's practical aspects, noting that the skills they acquired were valuable and directly applicable to their work placements.
The unit coordinator should enhance the practical side of the unit.
Feedback from Email and verbal feedback
Students complimented the format of lectures by combining drawing and modelling instructions where relevant and applicable.
The unit coordinator should follow the same teaching philosophy for the new unit development.
- Apply the formal principles of mechanical engineering design to translate user needs to design specifications
- Conceptualise and produce drawings of mechanical components and assemblies according to Australian Standards
- Use common Computer-Aided Design (CAD) software to model and render engineering components
- Analyse machine elements and explain the physical basis of their design, usage and safe operational limits
- Apply engineering design principles including limits, fits and tolerances to design, manufacture and assemble a machine component
- Work effectively in teams to professionally generate and communicate design concepts using suitable engineering terminology, symbols, and diagrams.
The Learning Outcomes for this unit are linked with the Engineers Australia Stage 1 Competency Standards for Professional Engineers in the areas of 1. Knowledge and Skill Base, 2. Engineering Application Ability and 3. Professional and Personal Attributes at the following levels:
Intermediate
2.4 Application of systematic approaches to the conduct and management of engineering projects. (LO: 3I 5I )
3.3 Creative, innovative and pro-active demeanour. (LO: 5I )
Advanced
1.1 Comprehensive, theory-based understanding of the underpinning natural and physical sciences and the engineering fundamentals applicable to the engineering discipline. (LO: 1A )
1.2 Conceptual understanding of the mathematics, numerical analysis, statistics, and computer and information sciences which underpin the engineering discipline. (LO: 1A 3A 4A )
1.3 In-depth understanding of specialist bodies of knowledge within the engineering discipline. (LO: 1A 2I 3A 4A 5A )
1.4 Discernment of knowledge development and research directions within the engineering discipline. (LO: 1A 2I 3I 4A )
1.5 Knowledge of engineering design practice and contextual factors impacting the engineering discipline. (LO: 1A 2A 3I 4A )
1.6 Understanding of the scope, principles, norms, accountabilities and bounds of sustainable engineering practice in the specific discipline. (LO: 1I 2A 3I 4A 5I )
2.1 Application of established engineering methods to complex engineering problem solving. (LO: 3A 4A 5A )
2.2 Fluent application of engineering techniques, tools and resources. (LO: 2A 4I 5I )
2.3 Application of systematic engineering synthesis and design processes. (LO: 1I 2I 3A 4A 5I )
3.2 Effective oral and written communication in professional and lay domains. (LO: 5A )
3.4 Professional use and management of information. (LO: 5A )
Note: LO refers to the Learning Outcome number(s) which link to the competency and the levels: N – Introductory, I – Intermediate and A - Advanced.
Refer to the Engineering Undergraduate Course Moodle site for further information on the Engineers Australia's Stage 1 Competency Standard for Professional Engineers and course level mapping information https://moodle.cqu.edu.au/course/view.php?id=1511
Alignment of Assessment Tasks to Learning Outcomes
Assessment Tasks | Learning Outcomes | |||||
---|---|---|---|---|---|---|
1 | 2 | 3 | 4 | 5 | 6 | |
1 - Written Assessment - 20% | ||||||
2 - Written Assessment - 30% | ||||||
3 - Project (applied) - 50% |
Alignment of Graduate Attributes to Learning Outcomes
Graduate Attributes | Learning Outcomes | |||||
---|---|---|---|---|---|---|
1 | 2 | 3 | 4 | 5 | 6 | |
1 - Communication | ||||||
2 - Problem Solving | ||||||
3 - Critical Thinking | ||||||
4 - Information Literacy | ||||||
5 - Team Work | ||||||
6 - Information Technology Competence | ||||||
7 - Cross Cultural Competence | ||||||
8 - Ethical practice | ||||||
9 - Social Innovation | ||||||
10 - Aboriginal and Torres Strait Islander Cultures |
Textbooks
There are no required textbooks.
IT Resources
- CQUniversity Student Email
- Internet
- Unit Website (Moodle)
- Computer with the Windows operating system
All submissions for this unit must use the referencing style: Harvard (author-date)
For further information, see the Assessment Tasks.
j.sul@cqu.edu.au
Module/Topic
Design Process & Design Cycle
- User needs and Design Specifications
- Understanding constraints, generating concepts, selecting the best concept
- Design thinking
Chapter
Events and Submissions/Topic
Module/Topic
Overview of Engineering drawings
- Introduction to AS1100: Technical Drawings, Part 101: General Principles
Details in engineering drawing
- Introduction to AS1100: Technical Drawings, Part 201: Mechanical engineering drawing
Chapter
Events and Submissions/Topic
Module/Topic
Geometric dimension and tolerancing & Failure under cyclic loading
- Case studies
- Recap of failure theories
Chapter
Events and Submissions/Topic
Module/Topic
Basics and design of shafts & Limits and fits
- Shaft layout
- Critical locations
- Other shaft components
Chapter
Chapter 7, Shigley
Events and Submissions/Topic
Module/Topic
Basics and design of rolling-contact bearings and gears
- Bearing types and life
- Selection of ball bearings
- Types of gears
- Terminology
- Force analysis
- Efficiency of gear trains
Chapter
Chapters 11 & 13, Shigley
Events and Submissions/Topic
Module/Topic
Chapter
Events and Submissions/Topic
Module/Topic
Assembly drawing and assembly in Autodesk Inventor
- Necessary information
- List of the parts needed
- Showing how to assemble the parts
Chapter
Events and Submissions/Topic
Module/Topic
Design of cams and flywheels, and Dynamic simulations in Autodesk Inventor
- Terminology in cams
- Fundamental law of cam design
- Fundamentals of flywheels
- Practical design considerations
Chapter
Chapters 16, Shigley
Events and Submissions/Topic
Module/Topic
Design of mechanical springs
- Stresses in Helical springs
- Deflection in Helical springs
- Modelling of mechanical springs
Chapter
Chapter 10, Shigley
Events and Submissions/Topic
Module/Topic
Couplings and Mechanical seal
- Static vs dynamic seals
- Ingress Protection rating
Chapter
Chapters 16, Shigley
Events and Submissions/Topic
Module/Topic
Practical basics of FEA and FEA in Inventor
- Finite element solution process
- Types of finite elements
- Boundary conditions
Chapter
Chapter 19, Shigley
Events and Submissions/Topic
Module/Topic
Selection of electrical motors and batteries
- Performance curves of DC motors and rated parameters
- Consideration of start-up torque
- Types of batteries
Chapter
Events and Submissions/Topic
Module/Topic
Future of technical drawings and sustainability in design
- Model-based definition that integrates CAD/CAM/CAI into a digital workflow
- Sustainable design embracing social, economic, and environmental impacts
Chapter
Events and Submissions/Topic
Module/Topic
Chapter
Events and Submissions/Topic
Module/Topic
Chapter
Events and Submissions/Topic
1 Written Assessment
Task 1: Create an engineering drawing template in A1 and A4 sizes in accordance with AS1100 using Autodesk Inventor Professional (DWG)
Task 2: Create a 3D model in Autodesk Inventor for the technical drawings attached separately.
Task 3: Create a technical drawing of the object given.
Task 4: Design a shaft under the given loading and layout conditions.
AI ASSESSMENT SCALE - NO AI
You must not use AI at any point during the assessment. You must demonstrate your core skills and knowledge.
GUIDELINES FOR AI TOOL USAGE FOR STUDENTS
The assessment should be completed entirely without AI assistance, usually in a controlled environment. However, even if the assessment is not conducted in a controlled environment (such as an online test), you must not use AI to complete any parts of the assessment.
You are allowed to use Grammarly or similar writing improvement tools to improve the quality of your assessment.
Week 5 Monday (11 Aug 2025) 11:59 pm AEST
Students to submit their report to the link provided in the unit's Moodle site.
Week 7 Monday (1 Sept 2025)
Students can access feedback through Turnitin Feedback Studio using the same link for submission.
Your work will be assessed against the following items:
1. Demonstration of a good understanding of AS1100.101 and .201 by using correct techniques in technical drawings
2. Understanding underlying theories to design and select the most suitable machine elements
3. Application of correct dimensioning and tolerances in technical drawings
- Apply the formal principles of mechanical engineering design to translate user needs to design specifications
- Conceptualise and produce drawings of mechanical components and assemblies according to Australian Standards
2 Written Assessment
Task 1: Design of a gear reduction mechanism
Task 2: Design of a mechanism for rotating-reciprocating motion
Task 3: Dynamic simulation of the design system
Task 4: Creating engineering drawings
AI ASSESSMENT SCALE - AI PLANNING
You may use AI for planning, idea development, and research. Your final submission should show how you have developed and refined your ideas.
GUIDELINES FOR AI TOOL USAGE FOR STUDENTS
Al may be used for pre-task activities such as brainstorming, outlining and initial research. You may use AI-assisted automatic speech recognition to transcribe notes, AI tools to convert notes into outlines, and AI tools to brainstorm or suggest improvements to already created work. Image generation technologies might be used to generate starting points for designs or tools used to explore possibilities for producing software. You must then use the AI-generated ideas as the starting point and apply your skills and knowledge to refine and improve the initial ideas to the final submission. No GenAI-created content without changes should be included in the final submissions.
You do not need to cite the AI-generated content, as it has been substantially changed in the final submission. However, you need to briefly describe how AI tools were used during the planning, research and initial idea-generation stage of the assessment.
Week 9 Monday (15 Sept 2025) 11:59 pm AEST
Students to submit their report to the link provided in the unit's Moodle site.
Week 11 Monday (29 Sept 2025)
Students can access feedback through Turnitin Feedback Studio using the same link for submission.
Your work will be assessed against the following items for each task.
- Task 1 (/25%)
Design requirement
Application of relevant analysis for shafts, gears, and the location of bearings based on the appropriate failure theories
Consideration of relevant materials for each machine element
- Task 2 (/25%)
Meeting the design requirements from the given input for the required output
Application of relevant analysis for reciprocating elements based on the appropriate failure theories
Consideration of relevant materials for each machine element
- Task 3 (/25%)
Modelling of each element in Autodesk Inventor
Part assembly and subassemblies for the final product in Inventor
Verfication of the mechanism designed using Dynamic Simulation in Inventor
Graphs and/or tables to demonstrate the results
- Task 4 (/25%)
Drawing for each element
Assembly drawing showing how all elements come together
Part list and BOM
- Use common Computer-Aided Design (CAD) software to model and render engineering components
- Analyse machine elements and explain the physical basis of their design, usage and safe operational limits
- Apply engineering design principles including limits, fits and tolerances to design, manufacture and assemble a machine component
- Work effectively in teams to professionally generate and communicate design concepts using suitable engineering terminology, symbols, and diagrams.
3 Project (applied)
Task 1: Design of a battery-powered mechanism with a cam and flywheels
Task 2: Design of a seal and non-linear analysis of the seal
Task 3: Stress analysis of the design for materials selection and dynamic simulation
Task 4: Creating engineering drawings
AI ASSESSMENT SCALE - AI PLANNING
You may use AI for planning, idea development, and research. Your final submission should show how you have developed and refined your ideas.
GUIDELINES FOR AI TOOL USAGE FOR STUDENTS
Al may be used for pre-task activities such as brainstorming, outlining and initial research. You may use AI-assisted automatic speech recognition to transcribe notes, AI tools to convert notes into outlines, and AI tools to brainstorm or suggest improvements to already created work. Image generation technologies might be used to generate starting points for designs or tools used to explore possibilities for producing software. You must then use the AI-generated ideas as the starting point and apply your skills and knowledge to refine and improve the initial ideas to the final submission. No GenAI-created content without changes should be included in the final submissions.
You do not need to cite the AI-generated content, as it has been substantially changed in the final submission. However, you need to briefly describe how AI tools were used during the planning, research and initial idea-generation stage of the assessment.
Exam Week Friday (24 Oct 2025) 11:59 pm AEST
Students are required to submit a report together with drawing and modelling files using the link provided in the unit's Moodle site.
Students can access feedback through Turnitin Feedback Studio using the same link for submission.
Your work will be assessed against the following items for each task.
- Task 1 (/25%)
Design requirement
Application of relevant analysis for cams, flywheels and the location of bearings based on the appropriate failure theories
Selection of a suitable electric motor and battery
- Task 2 (/25%)
Determining suitable O-rings and their materials
Determining the relevant gland and groove design for the chosen O-ring for your design
Conducting a non-linear analysis on the chosen O-ring and groove design
- Task 3 (/25%)
Applying correct boundary conditions in FEA and the process of choosing suitable materials
Verification of the mechanism designed using Dynamic Simulation in Inventor
Graphs and/or tables to demonstrate the results
- Task 4 (/25%)
Modelling of each element in Autodesk Inventor
Part assembly and subassemblies for the final product in Inventor
Drawing for each element
An assembly drawing showing how all elements come together
Part list and BOM
- Use common Computer-Aided Design (CAD) software to model and render engineering components
- Analyse machine elements and explain the physical basis of their design, usage and safe operational limits
- Apply engineering design principles including limits, fits and tolerances to design, manufacture and assemble a machine component
- Work effectively in teams to professionally generate and communicate design concepts using suitable engineering terminology, symbols, and diagrams.
As a CQUniversity student you are expected to act honestly in all aspects of your academic work.
Any assessable work undertaken or submitted for review or assessment must be your own work. Assessable work is any type of work you do to meet the assessment requirements in the unit, including draft work submitted for review and feedback and final work to be assessed.
When you use the ideas, words or data of others in your assessment, you must thoroughly and clearly acknowledge the source of this information by using the correct referencing style for your unit. Using others’ work without proper acknowledgement may be considered a form of intellectual dishonesty.
Participating honestly, respectfully, responsibly, and fairly in your university study ensures the CQUniversity qualification you earn will be valued as a true indication of your individual academic achievement and will continue to receive the respect and recognition it deserves.
As a student, you are responsible for reading and following CQUniversity’s policies, including the Student Academic Integrity Policy and Procedure. This policy sets out CQUniversity’s expectations of you to act with integrity, examples of academic integrity breaches to avoid, the processes used to address alleged breaches of academic integrity, and potential penalties.
What is a breach of academic integrity?
A breach of academic integrity includes but is not limited to plagiarism, self-plagiarism, collusion, cheating, contract cheating, and academic misconduct. The Student Academic Integrity Policy and Procedure defines what these terms mean and gives examples.
Why is academic integrity important?
A breach of academic integrity may result in one or more penalties, including suspension or even expulsion from the University. It can also have negative implications for student visas and future enrolment at CQUniversity or elsewhere. Students who engage in contract cheating also risk being blackmailed by contract cheating services.
Where can I get assistance?
For academic advice and guidance, the Academic Learning Centre (ALC) can support you in becoming confident in completing assessments with integrity and of high standard.
What can you do to act with integrity?
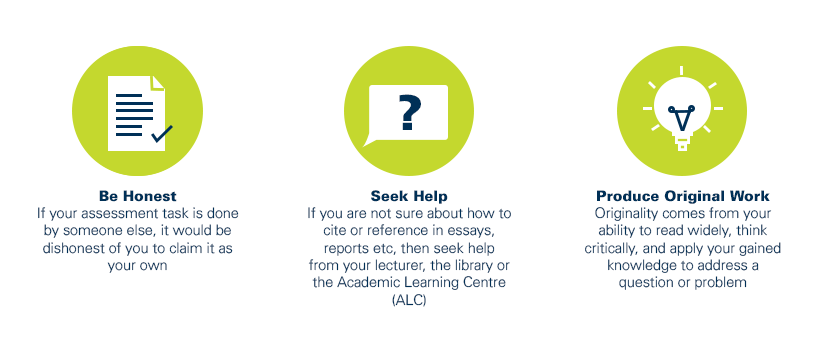